Mines researchers discovering new ceramic materials to support the hydrogen economy
Ryan O'Hayre and his team are focused on the development of protonic ceramics, with applications in all sorts of electrochemical energy conversion technologies
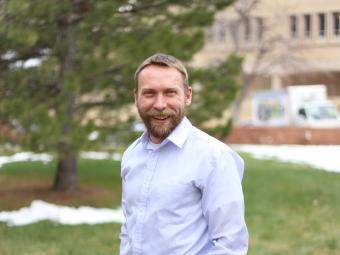
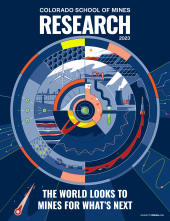
By Ashley Spurgeon, Special to Mines Research Magazine
Electrolysis plays a significant role in sourcing hydrogen for use in fuel cells and other energy technologies. But the ceramic materials used in the electrolysis process must withstand unique stresses and conditions to operate efficiently.
We sat down with Ryan O’Hayre, professor of metallurgical and materials engineering at Mines, to learn more about the ceramic materials he and his team of researchers at Mines are developing for this purpose and the many factors he must contend with when advancing this technology. Here’s what we learned.
Walk us through your research and how materials discovery relates to green hydrogen. What do you aim to do in your work?
Ryan O’Hayre: We’re developing a new class of materials called proton-conducting ceramics, or protonic ceramics. These have applications in all sorts of electrochemical energy conversion technologies. As it relates to hydrogen, you can use these in ceramic electrolyzers to take clean, renewable energy from solar or wind and water and split that water into hydrogen and oxygen.
There are some electrolyzers based on polymer materials that are great at operating at room temperature, and there’s also older ceramic materials used in solid oxide electrolysis cells that work at really high temperatures. The protonic ceramics we’re developing at Mines are in the medium temperature space, between 400 and 600 degrees Celsius. Being able to do electrolysis at these medium temperatures has a lot of potential benefits, because it’s a sweet-spot temperature-wise if you want to make more valuable things other than just hydrogen. These protonic ceramics are particularly attractive for making green synthetic fuels. We can do this by co-electrolysis where you don’t just split water into hydrogen, but you can split carbon dioxide into carbon monoxide at the same time. Then at these same magic intermediate temperatures between 400 and 600 degrees, you can do some clever chemical engineering to convince the carbon monoxide and hydrogen to react to make valuable fuels, such as alcohols and hydrocarbons.
What factors do you have to take into account when developing these ceramics?
O’Hayre: There’s a couple things we’re working on when developing the electrolyte, which is the ion-conducting membrane that’s the heart of the electrochemical device. This membrane has to conduct protons, but it needs to be electrically insulating. Just like in batteries, where a lithium ion conducting membrane is needed to serve as the heart of the battery, so same idea here.
For this membrane material, we want it to be as highly ionically conductive as possible but have very, very low electronic conductivity. It also needs to be mechanically strong enough to survive thermal cycling. We also need to figure out a way to make it as thin as possible, because that decreases the ionic resistance, so it makes the device more efficient. We can make these protonic membranes as thin as about 10 microns, and eventually we hope to be able to go down to maybe three or four microns.
And then on either side of this thin, dense membrane are electrodes that are also made out of ceramic materials, but they have to be porous so the reactants can diffuse into the electrochemical cell and the products can diffuse out. The electrodes must be electrically conductive and exceptionally catalytically active.
We’re developing new electrode materials starting from the periodic table and looking at different doping elements that we can put into these ceramics to make them more catalytically active and more electronically conductive. We create new ceramic compositions as paste or powders, and then we fabricate test cells that we test in our lab to develop the materials and see how well they perform and how durable they are.
Another key element of this is that we want these devices to not only run for a couple of hours — we want them to run for thousands and thousands of hours because that’s what you need for a commercial product. So we do these tests on the small scale in the lab, and once we’ve identified really promising materials, we pass them over to [other researchers on campus] who start making larger cells and stacks and do more long-term device testing.
What are the challenges you’re seeing when developing these ceramics?
O’Hayre: Just like with any other ceramic, they’re very fragile, and although you want to design an electrolysis device that’s going to run for 20 or 30 years, it can sometimes be challenging to get these ceramic devices to survive lab testing for more than a couple days. So mechanical strength, durability, reliability, lifetime, these are the biggest challenges. Another challenge is thermal cycling. An electrolyzer has to be able to follow the electric supply up and down depending on intermittent energy sources. It has to be able to ramp and sometimes it has to turn off completely and sometimes has to be operating full speed and sometimes it’s in between. These ceramics don’t really like having to heat up and cool down all the time, so that kind of thermal cycling can be a real problem. It’s these robustness and reliability issues that are the biggest constraint, the biggest challenge for ceramic electrolyzers.
How do you mitigate those challenges?
O’Hayre: It starts with fundamental property measurements in the lab. We measure their thermal characteristics. Like most materials, when you heat our ceramics up, they expand, so if you’re going to make an electrolyzer where you have these ceramic cells and are packaged inside some kind of metal frame which gets packaged in some type of box, if you don’t want to run into problems, then, ideally, all the different components in that box have to have the same thermal expansion characteristics so they all expand and contract at the same rate. There’s also the fundamental measurements of the mechanical properties. We will make a bunch of cells and break them on purpose to measure how much strength, how much force it takes to break them and then figure out modifications to make them stronger.
What would green hydrogen enable for the future of the energy transition and how we’re using energy?
O’Hayre: This is probably the single most important question, and it’s something the public really needs to understand. There have been a couple surges of interest in hydrogen that have fizzled out and everyone thought we’re going to be driving around fuel cell vehicles and clearly that’s not going to happen. So do we really need hydrogen? The answer is absolutely, yes. But it’s probably not for reasons that are readily apparent to the general public.
For a lot of our economy, we can pursue direct electrification — buildings, cars, lights — you can just use renewable electricity and use the grid and batteries, but there are certain sectors of the economy that are impossible to electrify. If we want to decarbonize those hard-to-decarbonize, hard-to-electrify sectors, that’s where hydrogen comes in. The big four industries are fertilizer production, plastics, cement and steel. Today, those four sectors are responsible for about 25 to 30 percent of all CO2 emissions, and you can’t only use electricity to produce them. The only way to remove fossil fuels from those big four sectors is with something like green hydrogen.
Why is Mines the ideal partner for solving the hydrogen challenge?
O’Hayre: We’ve had a long history in this field. The Colorado Fuel Cell Center has been around for close to 20 years, so we have a huge amount of infrastructure for electric chemical testing that’s almost unequaled by other universities in the U.S., spanning from the small button cell test stations that I have in my lab up to the 10, even 50, kilowatts scale test capabilities. At Mines, we have expertise in this field going all the way from the basic materials that go into these electrolysis devices all the way to the system-level engineering — allowing us to study how you would design a commercial system that would operate in thereal world. That’s a really unique capability, and it’s a result of 20-plus years of investment in this field.