Orediggers contribute to Colorado's PPE production efforts
Colorado School of Mines students and faculty are putting their ingenuity and engineering skills to work as part of a statewide effort to provide personal protective equipment to Colorado health care providers on the front lines in the fight against COVID-19.
Two Mines freshmen are among the makers firing up 3D printers across the state as part of Make4Covid, a coalition of Colorado manufacturers and makers working to provide health care professionals with the equipment they need.
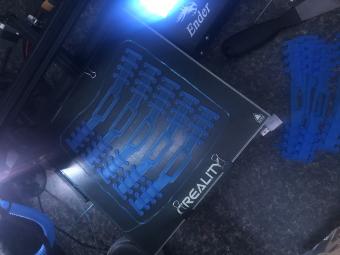
“Helping out has always been a part of my background,” said Samuel Wicklund, who is majoring in electrical engineering. “Since I have a 3D printer, lots of extra material, and enjoy helping others, I decided that I would start printing these surgical mask extenders as a way to help those who were risking their own health and safety as well as being away from family so that they could help others.”
The simple plastic extenders are designed to go around the back of the head – instead of attaching the elastic of a surgical mask around the ears, the wearer can attach them to the extender, for a secure yet more comfortable wear.
“After just a few hours of wearing the mask normally, the elastic starts to dig in and cut the skin of the ears,” said Wicklund, who is at home in Aurora. “As most nurses and other persons wearing these masks can go up to 12 hours of wearing them, it has been one of the items aside from face shields being heavily requested.”
Late last week, Wicklund was working on a batch of 225 extenders for a Denver-area hospital. Next on his list: 200-300 extenders for essential personnel at Buckley Air Force Base. He’s also printed a handful for his local fire department and plans to help make face shields as well.
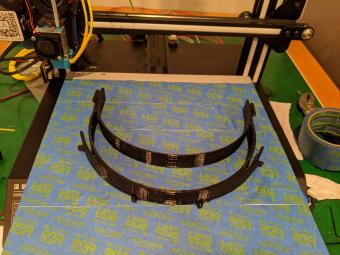
In Loveland, Paul Slayback, a freshman in engineering physics, is busy printing headbands for medical face shields. He encountered some printer issues last week but had things back up and running again Monday.
“I have the ability to help fight this pandemic and help the shortage of PPE,” Slayback said. “To do anything less would be a waste.”
Any 3D printer will work for making the headbands, he said, as long as it’s big enough. “There are preferred materials for printing, but they are mainly the more common ones so even cheaper printers can do it,” he said.
“Each band takes about two and a half hours to print, so I think I can reasonably get about eight to nine a day, if all goes smoothly,” Slayback said.
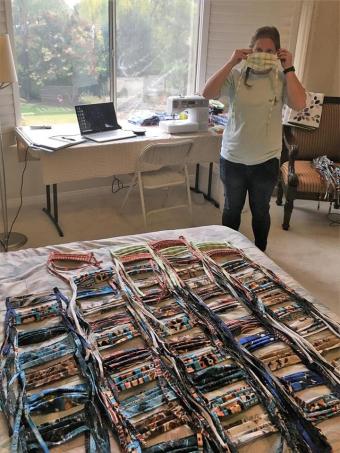
Slayback and Wicklund aren't the only ones getting involved in the effort. Among the other Orediggers helping to produce PPE:
Hannah Deahl '19, a master's student in engineering and technology management, has sewn more than 100 cloth face masks from her home in California. She sent 53 of them to her cousin, who is an Emergency Department doctor in Toledo, Ohio, and another 40 went to the Claremont Care Center in her hometown.
"I am a beginner quilter, which is what I usually use my machine for, but the need for masks outranks my hobbies, for now," Deahl said.
Chance Reeves, a senior in mechanical engineering, has already printed a few hundred "Montana Masks" for hospitals in Colorado and Wyoming, as well as friends and family. Intended to help extend the supply of N95 masks, the plastic masks were designed by a doctor at the Billings Clinic.
At his home in Westminster, Reeves has seven 3D printers. "I have been 3D printing for about 10 years, so I have collected them over that time," he said. "Some of them I’ve bought new, but most of them did not work properly and were given to me or I bought them for very cheap and repaired them. During the normal school semester, I work in the Makerspace in Brown repairing and maintaining the 3D printers there for students to use."
On campus, students and faculty in the Advanced Manufacturing Program are printing headbands for medical face shields, using the high-end equipment in the Advanced Manufacturing Teaching Lab, said Garrison Hommer MS ‘16 PhD ‘18, research assistant professor of mechanical engineering. Among those involved are Noah Mostow, Kelly Pickering and Steven Sullivan.
The Mines@Catalyst team is also collaborating with outside partners on a number of COVID-19 efforts, including PPE sterilization and reuse for hospitals facing shortages, director Judith Klein said.
A PPE drive led by Vice Provost John Bradford collected thousands of sterile gloves and hundreds of N95 and other masks from Mines research labs, for donation to Denver-area hospitals.
Orediggers: Are you involved in PPE efforts in Colorado (or elsewhere)? We want to know. Share your story at communications@mines.edu.
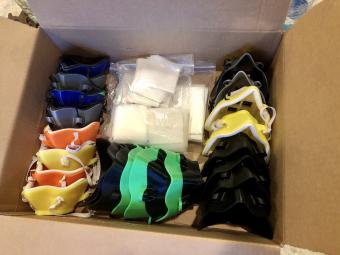